WorkSafeBC Part 5 Update (2025): Emergency-Planning Playbook for Hazardous Substances
Author: Angela Wheeler, CIH, CSP
Last updated: June 24, 2025
Executive Summary
- What happened? WorkSafeBC’s Board of Directors approved comprehensive amendments to Part 5: Emergency Planning in May 2024 which took effect on February 3, 2025.
- Who is affected? Every B.C. employer that manufactures, uses, or stores hazardous substances.
- What’s new?
- Plans must cover off-site as well as on-site consequences.
- A written chemical inventory—with locations and max quantities and container size—is now mandatory (BC OHS Reg 5.99).
- Annual reviews, worker participation, and documented drills are required (BC OHS 5.5 and 5.98).
- Penalties for non-compliance: WorkSafeBC can issue monetary fines and stop-work orders.
The Details
B.C.’s new rules raise the bar for emergency readiness. This article interprets the legal text and practical field experience into a checklist you can act on immediately.
Snapshot of the 2025 Amendments
Item | Requirement | Where to Find It |
---|---|---|
Effective date | 3 Feb 2025 | Board decision & OHSR update |
Review cycle | At least annually and after any incident | OHS Reg 5.98 |
Worker involvement | Plan must be developed in consultation with the joint health and safety committee / representative | OHS Reg 5.98 |
Scope | Applies to emergencies “arising within the workplace or in an emergency outside the workplace.” | OHS Reg 5.100 |
What Actually Changed?
New / Expanded Duty | Excerpt from Regulation |
---|---|
Broader scope | “Sections 5.98 to 5.104 apply in relation to an emergency arising within or outside a workplace …” BC OHS Reg 5.97 |
Inventory detail | “A written inventory … must list each hazardous substance present … maximum capacity of any container … the maximum quantity and location.” BC OHS Reg 5.99 |
Risk assessment depth | Must evaluate “existing and planned control measures … ability of workers to respond … estimated response time.” BC OHS Reg 5.100 |
Annual review + triggers | Update plan yearly or after any emergency, significant change, or invalidated risk assessment. BC OHS Reg 5.101 |
Worker training & drills | Written program plus records available to workers. BC OHS Reg 5.104 |
Chemical-Inventory Checklist (New Minimum Standard)
ProTip: Treat the inventory as a living document—update it when a new product arrives at the worksite and conduct a field verification of products at least annually. Use your SDS Management software to track inventories.
- Identify every hazardous substance capable of endangering a person in an emergency.
- For each product / chemical, record:
- Physical state (solid/liquid/gas)
- Maximum container capacity and max quantity
- Storage / process location
- WHMIS class + link to current SDS
- Include the inventory in the emergency-response plan so responders see it in context.
- Make the inventory readily available to workers, joint H&S committee members, and first responders.
Why Quantity Matters (Risk & Response Scaling)
Quantity Scenario | Risk Level | Typical Response Elements |
---|---|---|
≤ 25 L / kg of Toxic gas | Low–moderate | Local alarm, shelter-in-place; PPE |
> 200 L flammable liquid near ignition sources | High | Full evacuation, remote-shutoff valves, foam unit |
Bulk anhydrous ammonia (> 5 t) adjacent to residential area | Very high / off-site | CAER mutual-aid plan, public alerting, plume modelling |
Emergency Procedures Must Now Cover:
- Notification: Who gets the call (internal & external) and by what method.
- Protection & Evacuation: Clear decision tree: evacuate vs. shelter-in-place.
- Access Control: How to prevent re-entry and secure hot zones.
- Safe-Work Activities Post-Incident: Spill containment, waste disposal, re-entry criteria.
Training & Drills
- Initial orientation for all affected workers; refresh annually or when roles change.
- Drills: Plan drills at a frequency that matches the risk level—quarterly for high-hazard operations is a common best practice.
- Records: Keep attendance, lessons learned, and corrective-action dates.
Common Pitfalls (and How to Avoid Them)
Pitfall | How to Fix It Fast |
---|---|
Inventory only lists products, not max quantities. | Add a “quantity” and “container size” column in your spreadsheet. |
Plan ignores off-site locations. | Extend risk-assessment radius; communicate with local fire dept & local emergency services. |
Worker drills focus on fire, ignore chemical release. | Run mixed-scenario drills; include spill, toxic plume, & shelter-in-place. |
Documents locked in an office the fire department can’t access. | Store a digital copy accessible remotely and a hard copy at the entrance. |
Angela’s Action Plan for 2025 Compliance
- Download the official amendment package.
- Build or update your chemical inventory.
- Conduct a fresh risk assessment using the new criteria.
- Draft / update the Emergency-Response Plan—tie every section back to the inventory & risk assessment.
- Train workers and run at least one drill before your next annual review date.
- Set a calendar reminder to review the plan every 12 months or post-incident.
Resources for More Information
About the Author
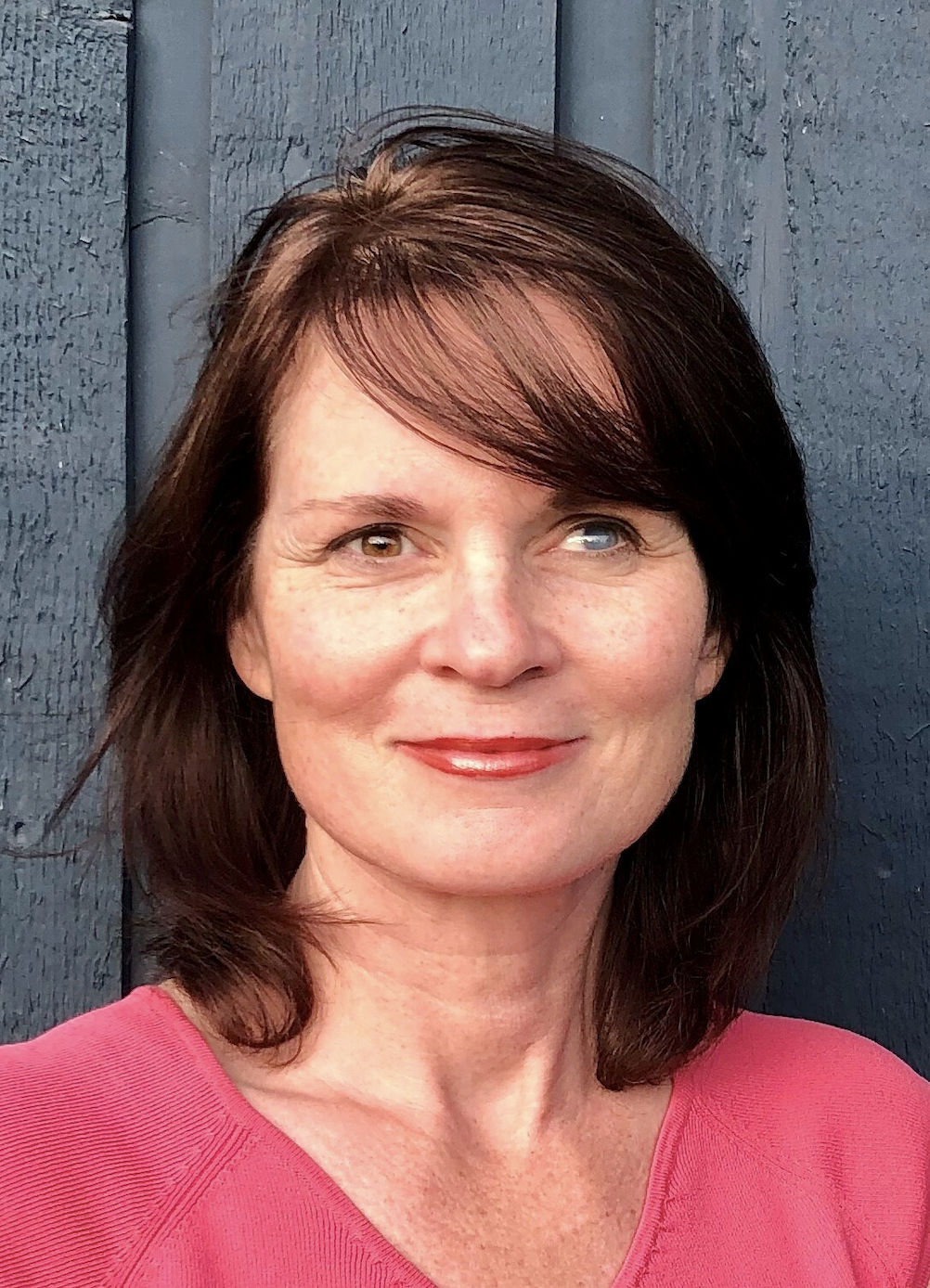
Angela Wheeler, CIH, CSP is a board-certified industrial hygienist and safety professional with over 25 years of experience helping Canadian employers navigate complex regulatory requirements. She has contributed to more than 200 emergency-planning projects for manufacturing, energy, and municipalities.
This guide is intended as general information and does not replace the OHS Regulation or legal advice. Always consult the official WorkSafeBC documents for complete requirements.